If you’re new to machining, the NC Shop Floor Programmer app in 3DEXPERIENCE can be really useful. It helps connect your designs with manufacturing, making it easier to program CNC machines directly. In this blog, we’ll give you a quick guide to get started with this app.
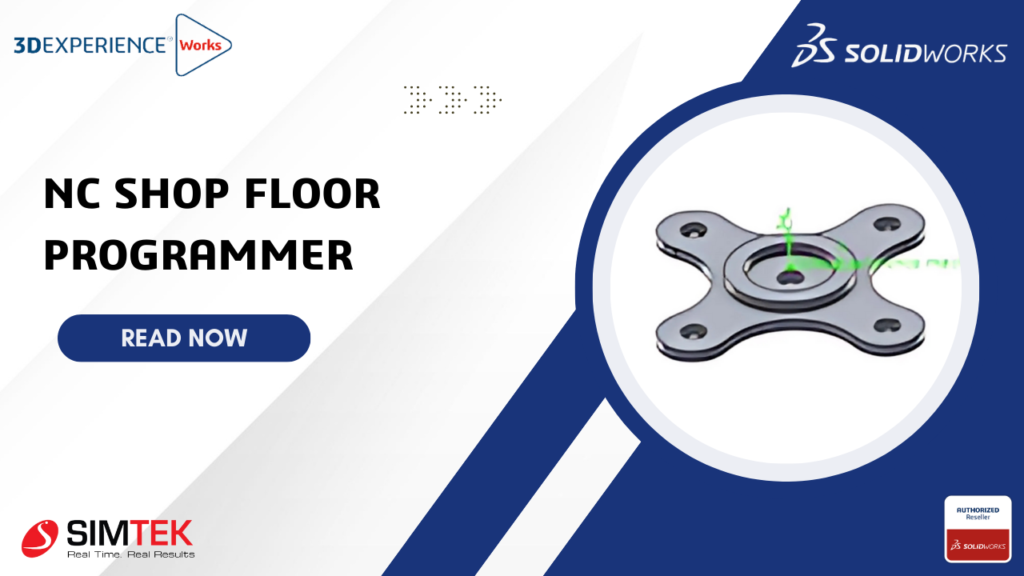
Introduction:
Shop Floor Machining on the 3DEXPERIENCE platform bridges the gap between the virtual and physical worlds of manufacturing. It allows you to create, optimize, and validate NC (Numerical Control) programs directly from your 3D models & Learn how the NC Shop Floor Programmer in 3DEXPERIENCE makes CNC programming simple and accurate. Import designs, simulate, and create programs easily!
key features:
Machine and Tool Management: Easily manage your machines and tools to suit your specific needs.
Stock Material Definition: Define the material you’ll be working with for accurate simulations and results.
NC Program Creation: Quickly generate complete NC programs. The software identifies machinable features and reuses previous operations, speeding up the programming process.
Simulation and Validation: Use advanced simulations to check your programs for any potential issues like accessibility and collisions before they happen on the shop floor.
NC Code Generation: Automatically create precise NC code, reducing errors and ensuring efficient machining operations.
Step-by-step process of using the NC Shop Floor Programmer in 3DEXPERIENCE SOLIDWORKS:
Step 1: Navigate to the NC Shop Floor App
First, you need to log into your 3DEXPERIENCE platform using your account credentials (username and password).
- Once you’re logged in, go to the 3DEXPERIENCE Dashboard.
- Look for the “Apps” section. Here, you’ll find a list of available apps.
- Search for “NC Shop Floor Machining” and click on it to open the app.
Step 2: Import Your 3D Model
- To begin programming, you’ll need to import a 3D model (usually from CAD software like SOLIDWORKS or CATIA).
- Click on “Import Model”, choose your file (like STEP, IGES, or CATPart), and load it into the app.
Step 3: Define the Machine and Tools
- Select the machine type you will use (like a 3-axis mill or 5-axis, CNC lathe).
Step 4: Define the Machining Part and Stock
Step 5: Define the Tools
Then, choose the tools (cutters, drills, etc.) you will use for the machining process.
Step 6: Feature Recognition
Step 7: Generate the Toolpaths
- Use the app to define the tool paths (the paths the cutting tool will follow).
- The software will automatically generate these paths, but you can adjust them if needed.
Step 8: Simulate the Machining Process
Step 9: Export the G-code
- Once you’re satisfied with the simulation, you can export the G-code (the set of instructions for the CNC machine).
- Save the G-code file and send it to your CNC machine for actual production.
Step 10: Monitor the Process
- After sending the program to the machine, you can monitor the progress and make adjustments, if necessary, directly from the app.
Step 11: Collaborate Share & Save
- You can share your work with team members in real-time, so they can review and provide feedback.
Benefits:
- Enhanced Efficiency: Streamline your machining processes with automated tools and reusable operations, which reduces programming time.
- Improved Accuracy: Validate programs with digital simulations to find and fix issues before they reach the shop floor.
- Seamless Integration: Connect design and manufacturing data to ensure consistency and reduce errors across your workflows.
- Collaborative Environment: Use the 3DEXPERIENCE platform’s cloud capabilities to work together in real-time with your team, no matter where they are.
Conclusion:
The Shop Floor Machining module on the 3DEXPERIENCE platform is a powerful tool for manufacturers to boost efficiency and accuracy. It uses advanced simulations, automated tools, and a collaborative environment to make transitions from design to manufacturing smoother, ensuring high-quality outputs and streamlined operations.