SOLIDWORKS FLOW SIMULATION
Computational Fluid Dynamics (CFD) Software
What is SOLIDWORKS FLOW SIMULATION and why is it needed?
SOLIDWORKS Flow Simulation is a software that accurately helps to simulate fluid (both liquid and gas flows) through the design and around the designs created. Dynamic feedback is provided based on the simulations and different capabilities are available like optimizing various parameters within the simulations. Whether it is to check for component overheating or icing, SOLIDWORKS FLOW SIMULATION delivers stellar results. The software is based on principles of computational fluid dynamics (CFD).
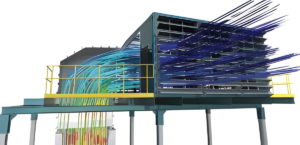
Many applications but one software
SOLIDWORKS Flow Simulation can be used to test for liquid and gas flow in many scenarios and applications like
- Heat exchangers
- Aerodynamic applications
- Heat flow and cooling needs in electronics
Thus, any ‘what if?’ questions are sorted through reliable simulations.
TOOLS
FEA Integration
Finite Element Analysis (FEA) helps to make a design robust and identify component failures and scenarios easily.Results and parameters from a CFD analysis can be used as inputs to FEA analysis. Impact on structural behaviour based on fluid behaviour and dynamics can be easily understood.
Rotating System Analysis
Optimize designs of rotating components like impellers and turbine blades.Simulations can be run based on the idea of a local rotating region, a global rotating region, single or multiple rotating reference frames.Reliable results can be achieved based on combinations of various factors like geometry, angular velocity, etc.
External Flow Analysis
External flow analysis finds use in the high number of real-world applications and design of critical components like ship hulls, airplanes, turbines, etc.Easy to set up different boundary conditions.Internal and external fluid flow dynamics can be combined to achieve holistic results
Internal Flow Analysis
Internal flow analysis finds application in designing pumps, valves, etc.Can solve both fluid and thermal problems that arise.Easy to use and intuitive to set up simulations in different scenarios
Free Surface Dynamics
Used in cases where there is a freely moving surface between two immiscible fluids (like air and water).Transient conditions can be simulated.The Volume of Fluid (VOF) is the underlying method used for calculations.Complex cases like sloshing in partially filled tanks, wave impact on solid bodies, etc can be studied
Electronics Cooling Module
It is an add-on to the SOLIDWORKS Flow Simulation software. Used extensively in design of chips and electronic components. Relation between current and heat generation can be easily understood to get a strong hang of thermal behaviour.
Particle Study
If fluids have particles in them, this can cause functional challenges (E.g., cat fines and dirt in crude, dust in air, etc.).The module helps to simulate erosion and other impact based on the nature of the particle and the material properties of the system.
Parametric Optimization
Powerful design tool. Helps map CFD studies with user-defined goals for the results. Complete CFD analysis offerings.
HVAC Module
Add-on module to simulation module. Advanced radiation simulation capabilities based on different materials. Brings consideration of human comfort factors, airflow optimization, etc.
FREQUENTLY ASKED QUESTIONS
How accurate is the SOLIDWORKS Flow Simulation software?
The software is as accurate as any general-purpose CFD program. There are validation examples that come with the installation that showcase the similarities between experimental and analytical results with results from Flow Simulation.
What are the hardware requirements for SOLIDWORKS Flow Simulation?
Processor: 3.3GHz or faster, Intel® Core i7, Xeon or equivalent AMD®
Operating System : Windows® 10 and 7 (2020 is the last year for Windows 7 support)
Memory: 16GB or more as required
Hard Drive: Solid State Drive (SSD) > 250GB, keeping 10% drive capacity free space
Graphics Cards: NVIDIA® Quadro® RTX 4000
Can we outsource computing?
Yes. Using the remote solving capability, users can send their Flow Simulation calculation to another computer on their network.
What kind of CAD data do I need to run Flow Simulation?
Since Flow Simulation is embedded in SOLIDWORKS, it can use any solid body geometry that was created or can be imported into SOLIDWORKS.
MATRIX
Flow SImulation |
HVAC MODULE |
ELECTRONICS COOLING MODULE |
|
Design Data Reuse | ![]() |
||
Multi-Parameter Optimization |
![]() |
![]() |
![]() |
SOLIDWORKS Flow Simulation Capabilities |
![]() |
||
Material Database |
![]() |
![]() |
![]() |
Internal – External |
![]() |
![]() |
![]() |
Heat Conduction in Solids |
![]() |
![]() |
![]() |
Gravity |
![]() |
![]() |
![]() |
Rotation |
![]() |
||
Free Surface |
![]() |
||
Symmetric | ![]() |
![]() |
![]() |
Gases, Liquid, and Steam |
![]() |
||
Boundary Layer Description |
![]() |
![]() |
![]() |
Mixing Flows | ![]() |
||
Non Newtonian Fluids |
![]() |
||
CAD Standards Checking (Design Checker) | ![]() |
![]() |
![]() |
Flow, Thermal, and Wall Conditions |
![]() |
![]() |
![]() |
Porous Components |
![]() |
![]() |
![]() |
Visualization | ![]() |
![]() |
![]() |
Results Customization | ![]() |
![]() |
![]() |
Communication & Reporting |
![]() |
![]() |
![]() |
Two-Phase (Fluid + Particles) Flows |
![]() |
![]() |
|
Noise Prediction (Steady State and Transient) |
![]() |
||
HVAC conditions | ![]() |
||
Tracer Study | ![]() |
||
Comfort Parameters | ![]() |
||
Electronic Conditions | ![]() |
||
Circuit Board Component Simplifications | ![]() |
||
Joule Heating | ![]() |